
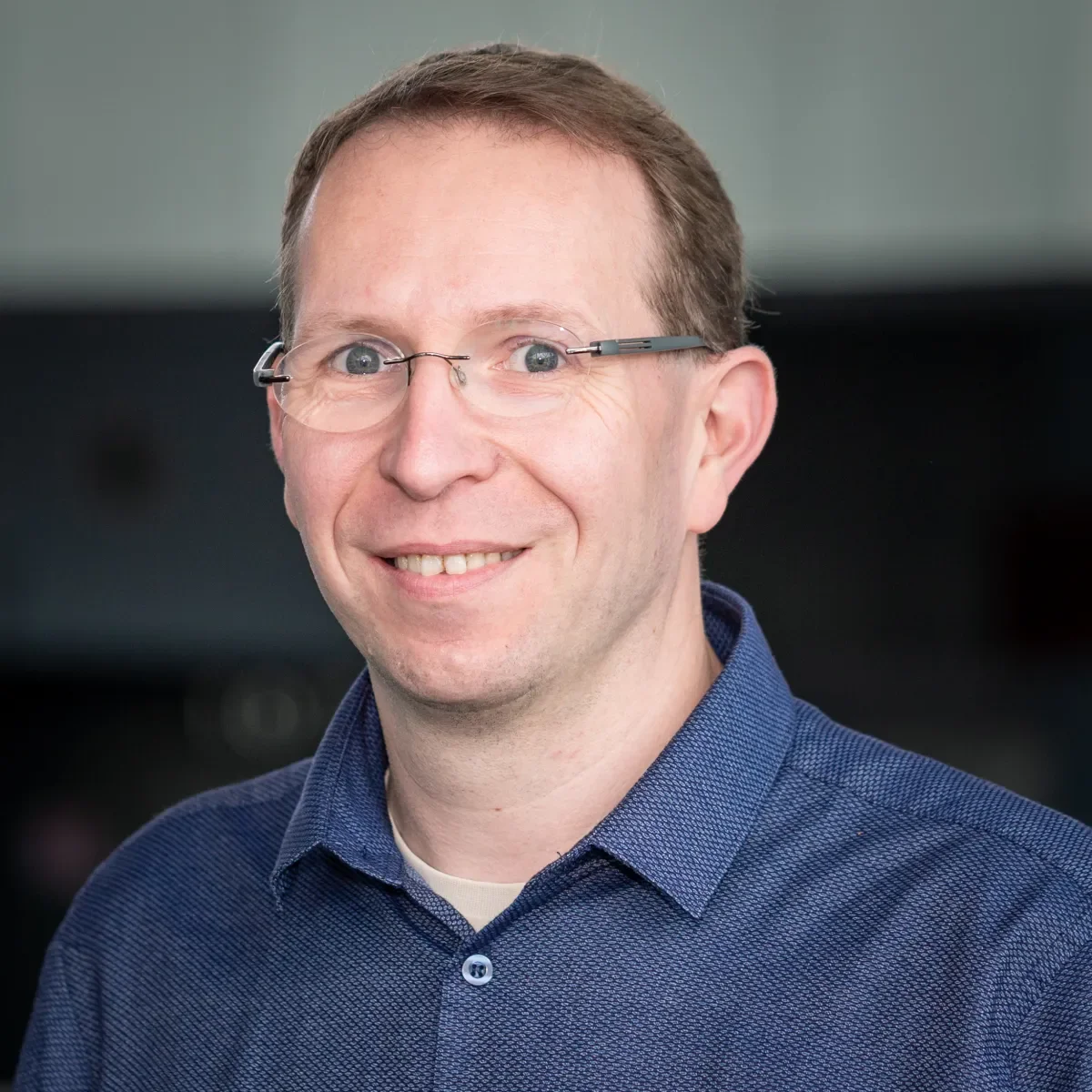
Searching for 'Rare Earth' Alternative
Indium Tin Oxide (ITO), is an excellent conductor of electricity and is transparent - two properties that ensure it is a crucial component for the working of mobile phones, flatscreens and solar panels. It’s also rare - a trace metal and byproduct of Zinc mining - and extremely expensive.
A cheaper substitute for ITO must be discovered before electronic and solar-cell based devices can be produced on a larger scale. This is the goal of Dr Karsten Fleischer, School of Physical Sciences, with the support of a new Science Foundation Ireland Frontiers for the Future grant, which he won with Professor Igor Shvets of Trinity College Dublin.
The first use of transparent and electricity conductive ITO was in the 1960s when it was incorporated as a component of the transparent windows on aeroplanes, to allow them to be heated without icing up.
In the 1970s and 1980s there was a huge demand for zinc, as it was used for corrosion protection on cars. This led to extensive mining for zinc worldwide and ITO was produced as a trace metal byproduct of that.
Expensive
“Indium Tin Oxide is a very useful material, and a key component of smartphones, solar cells and flatscreens, but it’s rare and expensive,” said Dr Fleischer. “It works well for a phone where you need to use it to cover a few cm2, but it’s far too costly to use if you need to cover 2,000 m2 with solar panels; about enough to generate power for your house.”
The touchscreen is one of the most expensive parts of a smartphone, while one of the most costly materials on the touchscreen is ITO. This makes it a critical material. However, it will not be financially feasible to use rare and very expensive ITO to meet the likely huge increase in the demand for smartphones, flatscreens and solar panels in coming years.
“If we want to be able to maintain the performance of our devices on a large scale, then a much cheaper alternative to ITO is required,” said Dr Fleischer. “It’s likely that we will have to massively upscale production of solar cells in coming years, for example, but we are not ready for that.”
There will not be enough ITO, at the right price, to meet expected future demand.
“We need to be ready for that, and transition to a new, cheaper alternative material, but we are not at that stage yet,” said Dr Fleischer. “We have probably left this 10 to 20 years too late, and so we will now need to make a dramatic and massive investment to be ready on time.”
Funding for research into finding an alternative to ITO, was funded by governments up to a few years back. These days the bulk of the support comes from private industry, who clearly see that progress on meeting future demand for electronics may be hampered by dependence on ITO.
With the support of the SFI grant, Dr Fleischer’s team will create new artificial materials in the lab, each one of which will potentially be an alternative to ITO. This will be done by combining two cheap materials in a layered new material and altering its composition every few layers.
Layers
The technology to make new materials by laying down alternate thin layers of existing materials in a new laminate through an atomic layer deposition tool, is located in the National Research Facility at DCU.
“These new materials are composite materials,” said Dr Fleischer. “We hope to make a material that has the same performance as ITO, but without using expensive materials. Of course in DCU we don’t have production capabilities, but we can show potential industry partners, through proof of concept methods, that it’s physically possible to do it.”
The plan is to approach big companies that make the deposition systems for applied materials towards the end of the four year SFI funding round. If all goes to plan, said Dr Fleischer, in perhaps 10 to 15 years' time we’ll have developed a material to replace ITO that can be used in bendable smartphones that don’t easily break or crack like current phones do.
It is important, said Dr Fleischer, that blue skies research identifies new materials that can replace ITO and that extensive tests are run before industry invests billions in changing its existing production processes.
“In four years’ time, at the end of this project, we want to be able to replace ITO with one of our new cheaper materials,” said Dr Fleischer.